3D打印技术:逐层堆积原理与多领域应用探析
19429202025-04-17生物科技7 浏览
从快速原型制作到个性化医疗植入物,3D打印技术正在重塑制造业与创新设计的边界。
一、3D打印的核心原理:逐层堆积的制造革命
3D打印技术的核心在于“逐层堆积”(Additive Manufacturing),即通过计算机控制,将材料逐层叠加形成三维实体。这一过程打破了传统减材制造的局限,无需模具即可实现复杂结构的精准成型。其工作流程可概括为以下步骤:
1. 模型设计:通过CAD软件创建三维数字模型,或利用3D扫描获取实物数据。
2. 分层切片:将模型分解为薄层(通常厚度为0.05-0.3毫米),生成打印机可识别的指令文件。
3. 材料堆积:打印头根据分层数据,通过熔融、固化或黏结等方式逐层叠加材料(如塑料、金属、树脂等)。
4. 后处理:去除支撑结构、打磨或热处理,提升成品精度与性能。
关键优势:
复杂结构易实现:传统工艺难以加工的镂空、曲面等设计,3D打印可轻松完成。
材料利用率高:仅消耗必要材料,减少浪费(传统制造浪费率可达90%)。
小批量生产经济:无需模具,单件与批量生产成本相近,适合定制化需求。
二、主流3D打印技术分类及适用场景

根据材料与成型方式,3D打印技术分为以下几类:
1. 熔融沉积成型(FDM)
原理:加热塑料丝(如PLA、ABS),通过喷嘴挤出后冷却固化。
特点:成本低、操作简单,适合教育、原型验证。
局限:表面粗糙,精度较低。
2. 光固化成型(SLA/DLP)
原理:紫外线照射液态光敏树脂,逐层固化成型。
特点:精度高(可达0.01毫米),表面光滑,适合珠宝、齿科模型。
局限:材料成本高,需避光操作。
3. 选择性激光烧结(SLS)
原理:激光烧结粉末材料(如尼龙、金属),形成致密结构。
特点:强度高、可打印复杂金属件,应用于航空航天、汽车零件。
局限:设备昂贵,后处理复杂。
4. 生物打印(Bioprinting)
原理:使用生物墨水(含活细胞)逐层构建组织或器官。
应用:人工皮肤、心脏瓣膜等医疗领域。
三、3D打印技术的多领域应用实例
1. 医疗健康:个性化治疗的新标杆
手术模型:根据患者CT数据打印器官模型,辅助术前规划(如复杂心脏手术)。
定制植入物:钛合金骨骼、牙齿矫正器,完美贴合患者解剖结构。
生物打印:可降解支架促进骨再生,未来或实现器官再生。
2. 航空航天:轻量化与高性能结合
发动机部件:GE公司采用3D打印的燃油喷嘴,重量减轻25%,寿命延长5倍。
卫星组件:镂空结构设计降低重量,提升燃料效率。
3. 建筑与制造:效率与创新的双赢
快速原型:汽车企业用3D打印验证设计,缩短研发周期50%。
建筑构件:迪拜“未来博物馆”外墙使用3D打印面板,减少施工时间与成本。
4. 消费与文化:创意无边界
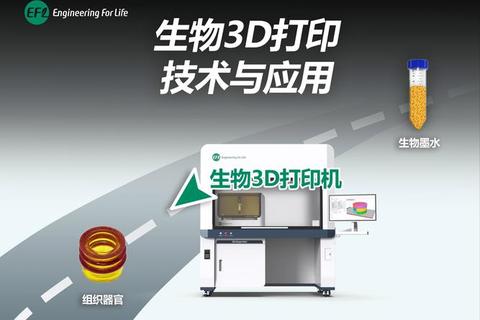
个性化产品:定制鞋垫、饰品,满足消费者独特需求。
文物修复:3D扫描与打印技术复原破损文物,如故宫青铜器。
四、3D打印的挑战与未来趋势
当前挑战:
材料限制:高性能金属、生物兼容材料仍依赖进口,成本较高。
规模化瓶颈:打印速度慢,难以满足大批量生产需求。
行业标准缺失:医疗等领域缺乏统一认证体系,制约商业化。
未来发展方向:
多材料融合:开发可同时打印金属与塑料的混合技术,拓展应用场景。
绿色制造:推广可回收材料,减少碳足迹(如废塑料再加工)。
AI优化设计:利用算法生成轻量化结构,提升性能并减少材料消耗。
五、实用建议:如何高效应用3D打印技术
1. 明确需求选技术:
教育/原型:选择FDM(低成本)或SLA(高精度)。
工业零件:优先考虑SLS或金属打印。
2. 材料适配性测试:
医疗领域需验证生物兼容性,建筑领域关注耐候性。
3. 设计优化技巧:
使用镂空结构减轻重量,节省材料(如航空航天部件)。
添加支撑结构避免变形,简化后处理流程。
4. 合作与资源共享:
中小型企业可联合第三方打印服务商,降低设备投入成本。
3D打印技术正从实验室走向产业核心,其逐层堆积的原理与跨领域应用潜力,为制造业、医疗、文化等行业提供了全新的解决方案。随着材料创新与规模化生产的突破,未来这一技术或将成为“第四次工业革命”的重要推手。企业需紧跟技术趋势,结合自身需求探索应用场景,方能在变革中抢占先机。