电子厂核心业务解析:生产流程与技术应用全览
19429202025-04-18性病资询8 浏览
电子制造业作为现代工业的支柱产业,其核心业务围绕精密的生产流程与前沿技术展开。本文将系统解析电子厂的核心生产流程、关键技术应用及行业趋势,为从业者、企业管理者及技术爱好者提供实用洞察。
一、电子厂生产流程全解析
电子产品的制造需经历从原材料到成品的多环节协作,每个步骤的精度直接影响最终质量。以下是典型电子厂的核心生产流程:
1. 原材料检验与预处理
关键步骤:对采购的元器件、PCB(印刷电路板)进行严格检测,包括尺寸、电气性能及可靠性测试,剔除不合格物料。
技术支撑:采用自动光学检测(AOI)设备快速识别缺陷,结合SPC(统计过程控制)确保一致性。
实用建议:建立供应商分级管理制度,优先选择通过ISO认证的供应商,并定期抽检以降低风险。
2. 表面贴装技术(SMT)流程
核心环节:
锡膏印刷:通过高精度钢网将锡膏涂覆至PCB焊盘,直接影响焊接质量。
贴片工艺:贴片机以微米级精度将元件贴装至PCB,高速机型可达每小时20万点。
回流焊接:通过温控曲线熔化锡膏,形成可靠焊点,需避免“虚焊”或“冷焊”。
技术挑战:微型化元件(如03015尺寸)对设备精度提出更高要求,需引入3D-SPI(锡膏检测仪)实时监控。
3. 插件与波峰焊接
手工插件:对无法贴装的过孔元件(如变压器)进行人工插装,依赖熟练工人。
波峰焊:通过熔融锡波完成通孔元件焊接,需控制锡液温度与接触时间以防止PCB变形。
4. 测试与品质控制
功能测试:通过自动化设备模拟产品使用场景,检测电路性能。
老化测试:高温高湿环境下长时间运行,筛选早期故障产品。
建议:引入MES(制造执行系统)实现测试数据全程追溯,快速定位问题批次。
5. 组装与包装
整机组装:将PCB、外壳、屏幕等部件集成,需防静电处理以避免元件损伤。
智能化包装:采用自动贴标机与扫码系统,提升出货效率。
二、关键技术应用与创新方向
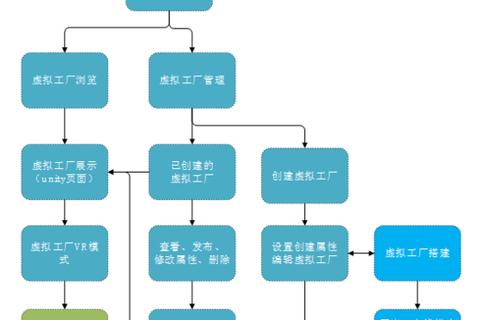
电子制造的技术演进正从自动化向智能化跃迁,以下为当前核心技术的应用场景:
1. 智能制造系统
MES系统:实时监控生产进度、设备状态及质量数据,实现动态调度与资源优化。例如,通过数据分析预测设备故障,减少停机时间。
工业互联网:设备联网后,可通过云端分析全局产能,支持跨工厂协同。
2. 先进工艺设备
高精度贴片机:采用视觉定位与压力反馈技术,贴装精度达±25微米,支持01005超小型元件。
激光加工技术:用于PCB微孔钻孔与精密切割,较传统机械加工效率提升50%。
3. 软件与数据驱动
AI质检:基于深度学习的视觉系统可识别焊点缺陷,准确率超99%,替代传统人工目检。
数字孪生:构建虚拟生产线模拟工艺参数,缩短新产品导入周期。
4. 绿色制造技术
无铅焊接:符合RoHS标准,减少环境污染。
能源管理:通过智能电表监控能耗,优化设备运行模式以降低碳足迹。
三、行业趋势与挑战
1. 技术升级压力
微型化与高密度:芯片封装技术向3D堆叠发展,要求设备具备纳米级精度。
材料瓶颈:高频高速PCB需使用低损耗基材(如PTFE),成本较传统FR4高3倍。
2. 供应链韧性需求
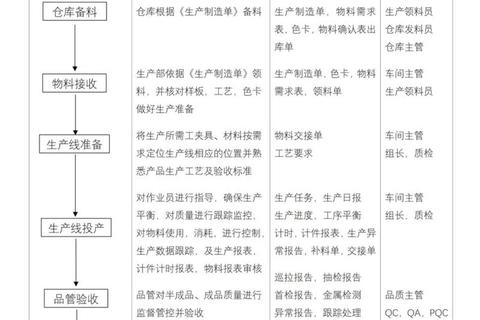
国产替代:半导体、高端电容等核心元件加速本土化,降低断供风险。
建议:建立“双源采购”策略,分散供应商依赖。
3. 智能化与柔性生产
工业4.0工厂:通过AGV(自动导引车)与协作机器人实现“黑灯生产”,人力成本降低70%。
定制化需求:小批量多品种订单增加,需快速切换产线,模块化设备设计成为趋势。
四、实用建议:提升电子制造竞争力的策略
1. 设备优化:定期升级老旧设备,引入双轨贴片机等高效机型,缩短生产节拍。
2. 工艺标准化:建立SOP(标准作业程序),减少人为失误,并通过DOE(实验设计)优化参数。
3. 人才培养:与高校合作开设“智能制造”课程,培养复合型工程师,同时内部推行技能认证体系。
4. 数据化转型:部署MES+ERP集成系统,打通从订单到交付的数据链条,实现精准排产。
电子制造业的竞争已从“规模扩张”转向“技术深耕”。企业需在流程精细化、技术智能化及供应链韧性上持续投入,方能在产业升级浪潮中占据先机。未来,随着AI、5G与量子计算的融合,电子厂的核心业务将向更高附加值领域延伸,成为推动全球科技革新的核心引擎。